Fasteners and Machining: Secret to Effective and Trustworthy Manufacturing
Fasteners and Machining: Secret to Effective and Trustworthy Manufacturing
Blog Article
Unveiling the Intricacies of Bolts and Machining Processes for Optimal Efficiency
In the world of design and production, the selection of fasteners and the intricacies of machining processes play a crucial duty in figuring out the supreme performance and longevity of a product. From the seemingly uncomplicated job of choosing the ideal kind of fastener to the facility accuracy machining strategies used, every action in this procedure needs careful interest to detail. As we begin on this exploration into the world of bolts and machining, we will certainly discover the subtle yet essential aspects that can significantly affect the performance and high quality of the final product, losing light on the frequently ignored facets that can make all the difference in attaining ideal performance.
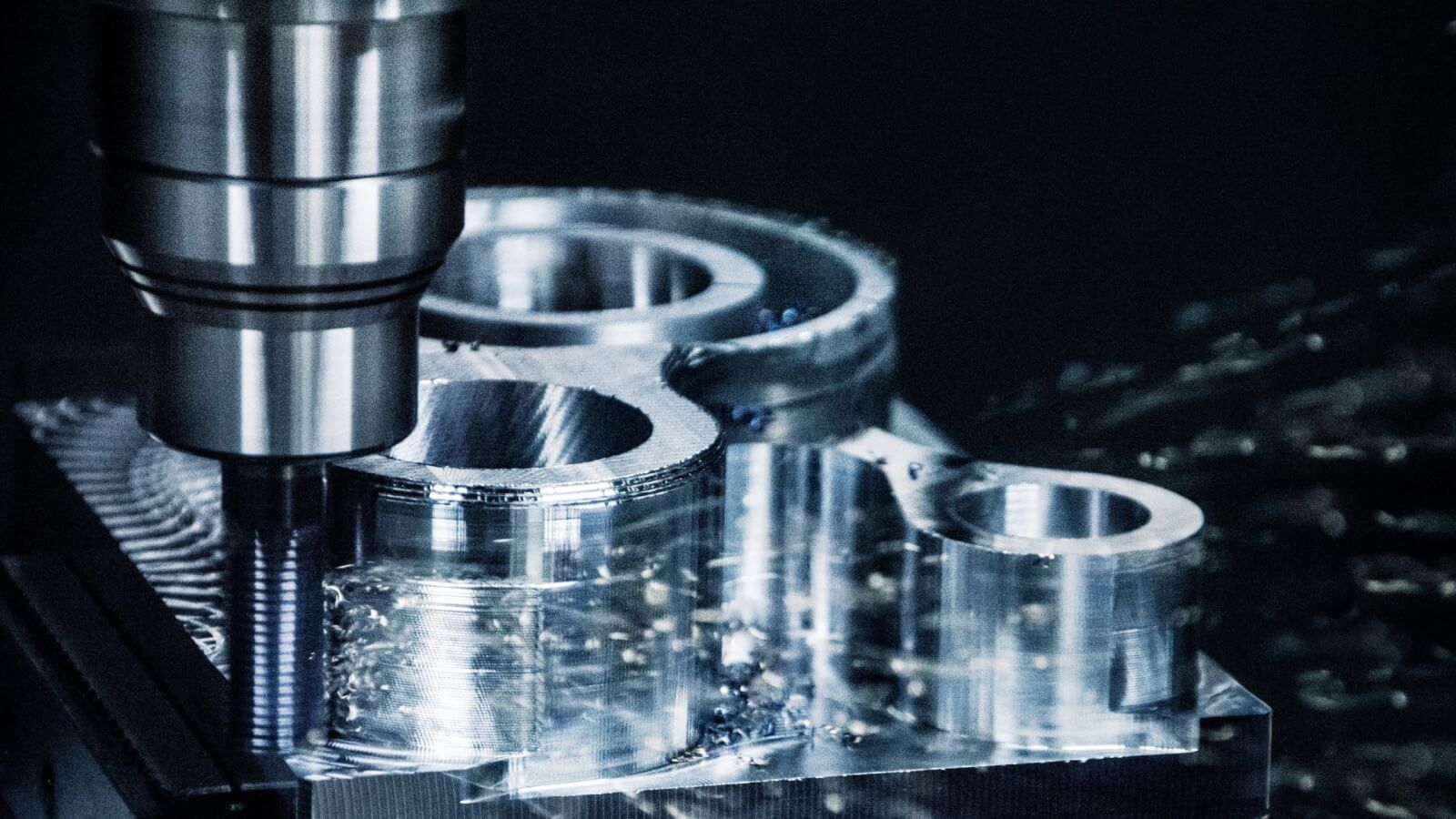
Relevance of Appropriate Bolt Choice
Choosing the appropriate bolts is critical in making sure the architectural honesty and durability of any mechanical setting up. Fasteners play a fundamental duty in holding components with each other safely, with the right choice adding significantly to the general efficiency and reliability of the assembly. When picking bolts, elements such as material compatibility, ecological conditions, load-bearing ability, and ease of setup must be very carefully taken into consideration to guarantee optimal efficiency.
Incorrect fastener selection can cause a series of issues, including helping to loosen, corrosion, and even structural failing. Utilizing bolts that are not fit to the certain needs of the setting up can endanger its functionality and pose security risks. Designers and engineers have to diligently examine the application needs and select fasteners that satisfy or surpass the needed requirements and specifications.
In addition, the appropriate bolt selection process entails evaluating the joint design, prepared for tons, vibration degrees, and prospective thermal expansion or tightening to guarantee that the picked fasteners can endure the operating problems efficiently. By focusing on correct fastener option, manufacturers can enhance the high quality, longevity, and performance of their mechanical assemblies.
Types and Attributes of Bolts
A vital element of mechanical settings up hinges on understanding the diverse types and one-of-a-kind attributes of fasteners made use of in various commercial applications. Bolts are vital elements that hold frameworks with each other, ensuring security and capability. There is a vast array of bolts available, each created for certain functions based on the application demands. Common sorts of fasteners consist of screws, bolts, nuts, washers, pins, and rivets.
Screws are threaded bolts that are commonly used to sign up with two or even more components with each other. Screws are comparable to screws but are typically used with a nut to create a secure joint. Nuts are internally threaded bolts that mate with screws to hold parts together. Washing machines are slim plates that distribute the lots of a fastener, protecting against damages to the material being attached. Rivets are irreversible fasteners that are hammered or pushed right into location. Pins are used for positioning or to secure components temporarily.
Understanding the features of each type of bolt is crucial for selecting the best one for a particular application, making sure ideal efficiency and reliability of the mechanical setting up. Fasteners and Machining.
Accuracy Machining Strategies for Performance
The complex design needs of different fasteners demand utilizing accuracy machining strategies for optimal effectiveness in producing processes. Precision machining is important in making certain that fasteners meet the specific requirements needed for their designated application. Among the main techniques utilized in accuracy machining is Computer system Numerical Control (CNC) machining, which enables high levels of precision and repeatability in the manufacturing of bolts. CNC devices are qualified of performing complicated cuts and shaping procedures with very little human intervention, bring about raised efficiency and uniformity in see here now the manufacturing process.
In addition to CNC machining, various other accuracy techniques such as grinding, milling, and turning are commonly utilized to achieve the limited resistances required for fasteners. These methods permit makers to create bolts with smooth surfaces, precise measurements, and high architectural stability. By utilizing accuracy machining strategies, suppliers can boost the high quality of bolts, decrease material waste, and boost general manufacturing efficiency. In addition, the use of innovative machining procedures aids make certain that fasteners fulfill sector standards and customer expectations for efficiency and dependability.
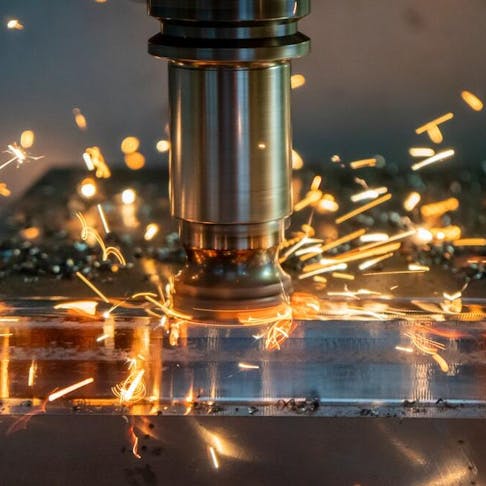
Variables Affecting Machining Refine Performance
Different variables play a considerable function in establishing the efficiency of machining procedures in the manufacturing of fasteners. Enhancing these parameters based on the particular needs of the bolt being generated is essential to accomplishing exact and affordable machining.
Maker strength and security also play an important duty in figuring out machining procedure efficiency. An experienced operator can make real-time changes, troubleshoot problems efficiently, and make certain that the machining procedure runs smoothly, eventually affecting the final quality of the bolt.
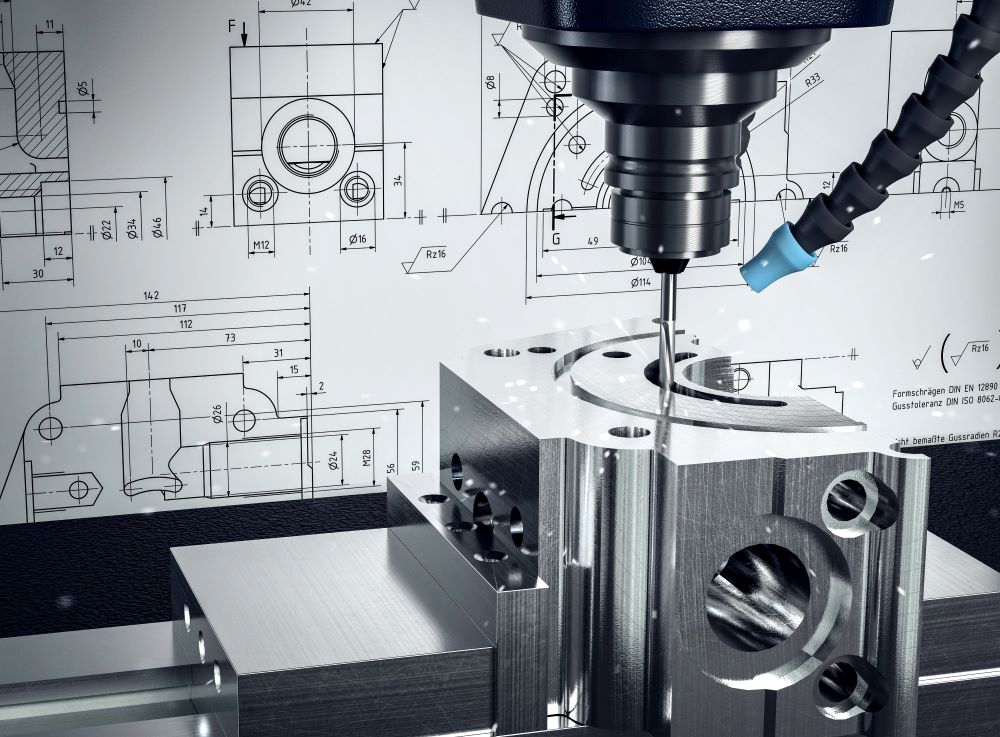
Quality Assurance Actions in Manufacturing
Factors affecting machining process performance, such as cutting tool selection and machine stability, directly impact the execution of quality control steps in manufacturing. Routine maintenance of machining equipment is additionally essential to maintain top quality control. By sticking to rigorous quality control measures, makers can improve customer satisfaction, build a track record for reliability, and ultimately attain optimum performance in their machining processes.
Final Thought
To conclude, selecting the best bolts and using precision machining strategies are important for optimal efficiency in manufacturing processes. Recognizing the types and features of fasteners, in addition to factors affecting machining procedure efficiency, can cause improved efficiency and quality assurance actions. By taking explanation notice of these details, producers Discover More Here can accomplish higher levels of efficiency and dependability in their items.
In the world of engineering and manufacturing, the choice of bolts and the intricacies of machining processes play a pivotal function in figuring out the best efficiency and toughness of a product (Fasteners and Machining). One of the primary techniques used in accuracy machining is Computer Numerical Control (CNC) machining, which allows high levels of precision and repeatability in the production of bolts. The use of advanced machining processes helps make sure that fasteners satisfy industry requirements and consumer expectations for performance and dependability
In conclusion, selecting the best fasteners and utilizing accuracy machining strategies are crucial for optimal efficiency in manufacturing processes. Recognizing the types and features of fasteners, along with aspects influencing machining procedure efficiency, can lead to improved effectiveness and top quality control steps.
Report this page